The primary processing method used for spodumene lepidolite is beneficiation. This involves removing impurities such as quartz and gangue (the unwanted materials that accompany the mineral). The final product is a purer form of spodumene lepidolite that can be sold on marketplaces around the world.
There are a number of mining equipment used for the extraction and beneficiation of spodumene lepidolite. Primary among these are earthmoving equipment, such as bulldozers and backhoes, as well as plant and machine tools used for breaking up the rock. In order to maximize the recovery of lepidolite, other processing steps may also be employed, such as flotation or washing.
The beneficiation of spodumene lepidolite concentrates is a critical step in the mining process. The ore must be processed to remove all impurities, including gangue and other non-metallic minerals, before it can be turned into high value products such as sapphire and ruby.
The most common beneficiation method is the froth flotation technique. Froth flotation uses a froth of bubbles to break down the mineral particles and separate them from the water phase. The floating mineral particles are then caught by a filter and removed from the mixture.
Depending on the purity of the lepidolite concentrate, other processing steps may be necessary. These include heat treatment, evaporation, adsorption, and clarification. Heat treatment helps to temper the spodumene so that it does not become brittle during further processing. Evaporation removes water from the concentrate to create a more dry product.
Adsorption removes pollutants or other materials that do not dissolve in water vapor formads an insoluble residue called “adsorbates”. Clarification separates crystalline material from non-crystalline material by using a filtration process.
One of the most abundant and valuable mineral resources on Earth is spodumene lepidolite. The crystal form of this mineral, spodumene, is a beautiful blue color. Spodumene lepidolite has been found in all parts of the world and is usually associated with hydrothermal deposits. The production of spodumene lepidolite begins with the extraction of natural gas from shale formations.
After the gas is processed, it is transported to various processing plants. Spodumene lepidolite mining beneficiation processing equipments in south africa makes this process much easier. The equipment separates spodumene from other minerals, such as feldspar, by way of a Supercritical Fluid Reaction (SCRF) process.
The SCRF process uses high-pressure and heat to break down minerals into their elemental forms so that they can be more easily removed. This method is much faster and cleaner than traditional mining methods, which can leave behind environmental liabilities.
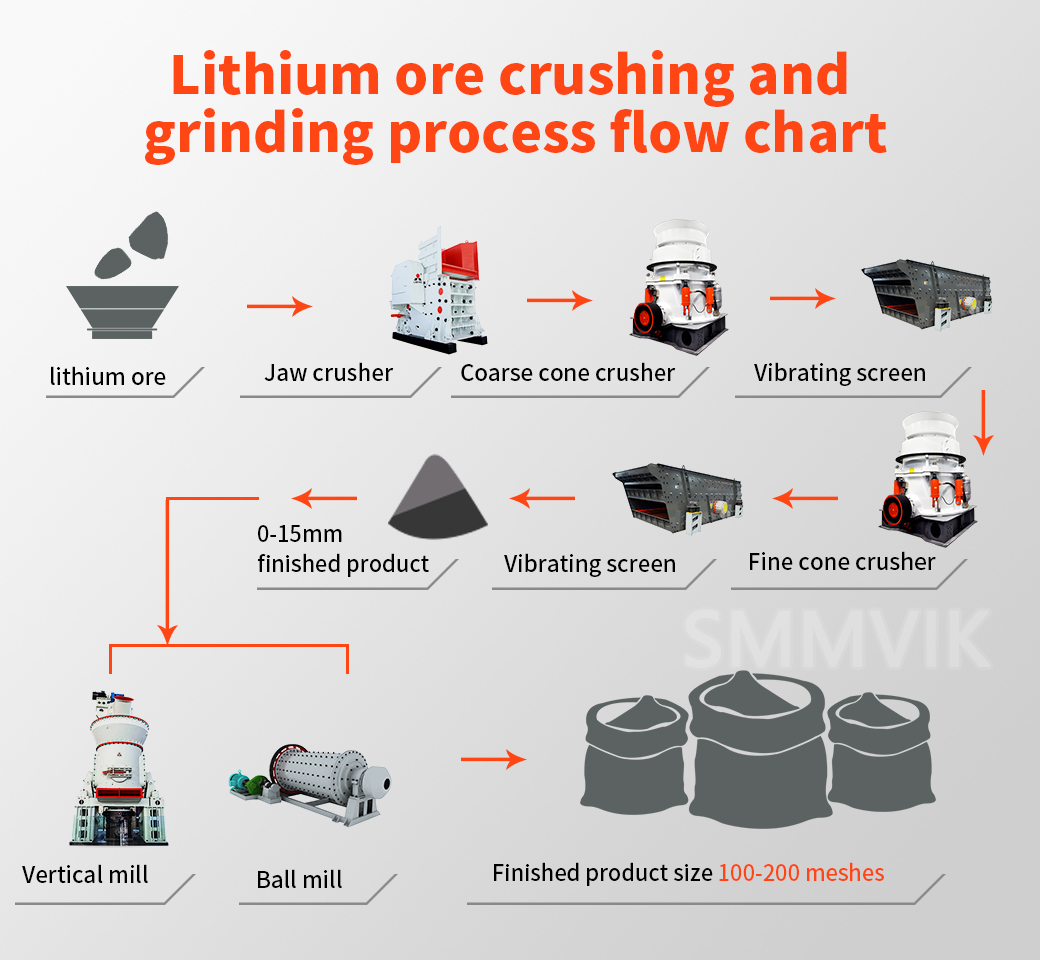
Processing of mineral ores is an integral part of mining operations. A wide variety of minerals can be mined, and processing is required to extract the desired product from the ore. The most common type of processing operation is smelting, which uses a furnace to convert the ore into a metal. Smelting also produces waste material that must be eliminated from the process.
After smelting, the next step in the mining process is extraction. This involves extracting the valuable minerals from the ore using various methods. Extraction can involve grinding the ore, using a crusher or a hammer mill, or drilling and blasting away pieces of the ore.
Once extraction is complete, the final step in mining is concentration. Concentration involves removing all non-mineral substances from the processed ores so that only the desired minerals are left. This can be done by dry washing, flotation, or gravity separation.
Mining processes always produce waste material that must be eliminated before production can resume. Processing equipment for spodumene lepidolite mines must remove contaminants such as sulfur dioxide and nitrogen oxide gas while preserving other valuable elements in order to meet environmental regulations.
The most common method used to remove these gases is flotation. Flotation separates heavy metals and other contaminants from lighter minerals by using bubbles of air and water to carry them away from the mine site. The lightweight minerals are then returned to the mine site for further processing.