Stone chips: also known as stone powder, are produced during the process of mining stones, processing concrete with sand, often treated as waste material, and then found to be sortable, processed as mechanism sand;Mechanical sand: by non-weathering, soft rock stone, waste concrete as raw material processing, particle size ≤4.75mm sand particles, can be sold or used in construction, road, railway and other fields.
Natural river sand is being exploited restrictively, and urban development still requires large amounts of aggregate, from which do sand for construction come? At first there is the mechanism sand is excavated, applied, and then there is stone dusts reused, so what is the difference between the two? How then should the sand production process be conducted? See below.
1. Distinction between stone dusts and mechanism sand.
01. the granulotype differed:Mechanism sand is subjected to reasonable processes such as crushing, sand preparation, and sieving, and the grain type is basically cubic in shape; Stone chips did not undergo targeted processing, and the grain type was irregular and angular;
02. particle size different:The stone chips differ in particle size size, doped in the range of 2.36 mm-4.75 mm, and the gradation is highly implausible; Mechanism sand is processed to different particle sizes and uniform sizes according to different process requirements;
03. with varying quality:Stone chips with particle size less than 0.16 mm stone meal content, mud content, etc, are high, and their surface is rougher than sand; Mechanism of rational process production sand rock powder content and mud content meet the criteria for sand used in construction, and the compressive strength of stone is high.
2.Introduction of stone chip and machine sand production process.
Stone chips need to be treated by a specific process and can be used as mechanism sand, while stone materials similarly need to be fed, broken, sand preparation, sieving and other production processes before becoming mechanism sand, and the specific sand production process is as follows.
Introduction of stone chip sand production process:
Shaping: the stone debris collected by the conveyor to the stone shaping machine (impact sand making machine, hammer crusher, etc.) at the first deep processing, improve the angular, irregular grain type;
Powder selection: dry sand process is to use the powder separator to recover 0.075mm stone powder in stone debris, reduce the content of stone powder in the finished product, and then screen, distinguish the finished product specifications;
Sand washing: the wet sand process is to screen out the 3-6mm and 0.075-3mm finished products, and then use the sand washing machine and water to remove the impurities of the finished products, reduce the mud content, etc.
Note: users only need to choose one between powder selection and sand washing.
Feeding: the mined stone is generally transported to the bin, and then fall on the vibration feeder, or directly put on the feeder by the excavator, in the simple screening size specifications into the coarse crusher;
Crushing: a coarse crushing machine (jaw crushing machine) will preliminary process the stone with a particle size gauge of 500-800 mm; Another 5-50 mm treated by a medium crushing machine (counter fracture machine or cone crushing machine);
Sand making: sand making equipment (impact sand making machine, fine crusher, etc.) can treat stones below 50mm into mechanical sand < 4.75mm, and then coordinate with vibrating screen to strictly control the particle size of finished products.
Note: a process to increase sand washing can be chosen on demand.
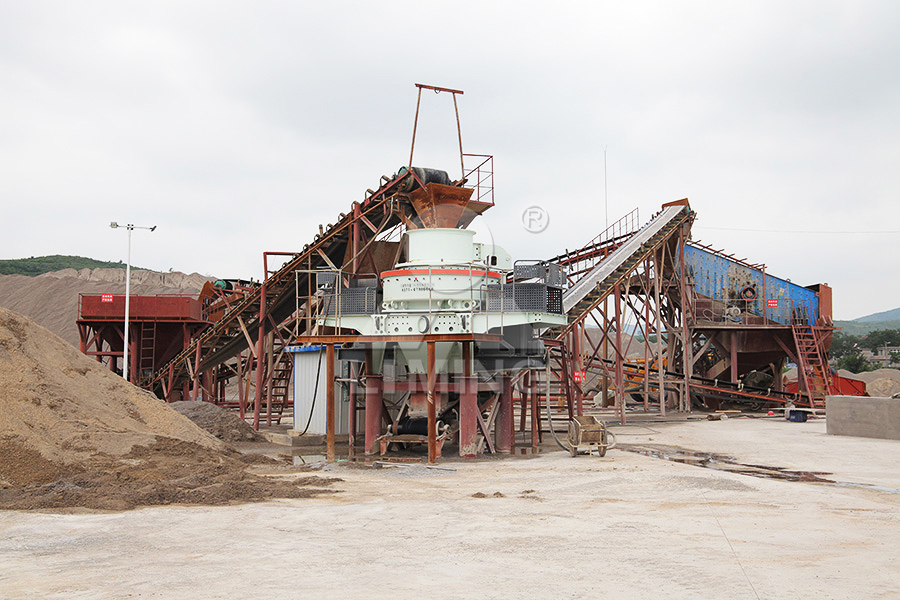
3. Stone debris and mechanism sand production equipment where to sell?
Sand making machine, jaw crusher, impact crusher, cone crusher, etc, are indispensable equipment for stone chip Sand making and machine-made Sand production. How its technology and quality can affect the income of the whole line, so it is necessary to consider the choice of manufacturers. SMMVIK Machinery is recommended here, for the following reasons:
01. advanced technologies.
Professional R & D personnel coupled with the continuously introduced domestic and foreign technologies, vertical numerical control plant beds, strive for equipment to meet user needs, improve benefits, and reduce consumption;
02. reliable quality.
Equipment is cast from the body to vulnerable using high-quality alloy materials, and even the casting of parts is lean, reducing the failure rate to even lower;
03. service improvement.
Early equipment recommendation, process design, process planning, accompanied by the middle of the installation, debugging, operation, training, operation, pays a return visit regularly, long-term quality assurance, in the late original accessories, can help each user worry for production!